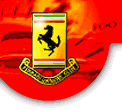 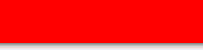
|
 |
 |
 |

Ferraris : Expensive to buy, Expensive to build
8.5.00
It is logical to conclude that a new Ferrari 550 Maranello costs L365 million (E188,584)
in Italy simply because it is fast and sexy.
A Ford Mondeo, on the other hand, is neither and therefore justly deserves its lowly
L37.3 million base price.
Obviously, this is a gross simplification, as a recent trip to Ferrari's headquarters
here revealed. The astounding price tags of Italian sports cars have more to do with
the way exotic cars from the region have been assembled for the past 50 years. It is
a labour-intensive process that heaps on cost at every level and has changed little
through the years.
For example, consider the pile of steel sheets and tubes that is the basis of a Ferrari
550 chassis. Before anything else happens, the raw material must be trucked miles
up narrow, winding roads into the Apennine mountains to Ferrari's chassis supplier,
Vaccari & Bosi Srl.
The company, which has built Ferrari chassis for five decades, is near the village
of Pievepelago because the owner, Signor Bosi, was born there and likes the view.
The plant is next to a river and a 2,000-year-old Roman stone bridge.
Bosi's 70 employees work on assembly lines that are a collection of welding guns,
grinders, cutters and hand-operated jigs for fixing the steel in exactly the right
position. Each line is responsible for one of Vaccari & Bosi's customers, which
include Ferrari, Lamborghini, Maserati and the new Qvale Mangusta.
Vaccari & Bosi fabricate everything from the raw sheets and tubes, including the
jigs themselves, to ISO-9002 standards. There are no economies of scale with this
process; costs rise in line with the number of parts to be made.
A single Ferrari chassis has more than 900 hand-cut and bent pieces held together
by more than 3,000 welds - all done by hand.
Bosi supplies other metal components to the 550, including fuel tanks, mufflers,
intake stacks and exhaust headers. Unlike the cast-iron headers of mainstream cars,
a Ferrari V-12 exhaust manifold is composed of equal-length stainless steel tubes
that are painstakingly pulled and bent at the same time.
The process prevents wrinkling where the metal curves and results in an elegant
spaghetti of smooth pipes that flow gases more efficiently than manifolds with
wrinkles or casting flash.
Ferrari does most of its own engine part machining with modern computer controlled
machines. They quickly reduce a 550's forged-steel crankshaft from 72kg to its
final weight of 21.5kg. Afterwards, however, workers break out the hand tools
to grind off any flash and put the final polish on the bearing journals. It is
a delicate process that lasts hours.
Once a 550 reaches the assembly line, each car spends about 45 minutes at each
station, of which there are dozens. Workers pull parts off a single trolley
that follows each car down the line. Next door, seamstresses in the upholstery
shop stitch together the hundreds of separate leather interior pieces and glue
them over plastic substrates, which then are placed on a trolley.
Interestingly, although many people believe Ferrari interiors are hand-stitched,
things aren't quite that Old World. Pushing a needle through leather is brutal
on the fingers, so almost everything is sewn on machines.
For 2000, Ferrari expects to build 11.5 cars a day, most of which are the
lower-priced 360 Modena model that begins at L230 million. Six hundred 550
Maranellos will be assembled this year out of a total output of 3,600 cars.
No doubt, exclusivity is also a major component of the price.
Acknowledgement: Aaron Robinson, Automotive News Europe
Click here to return to the Ferrari Happenings page.
|
|